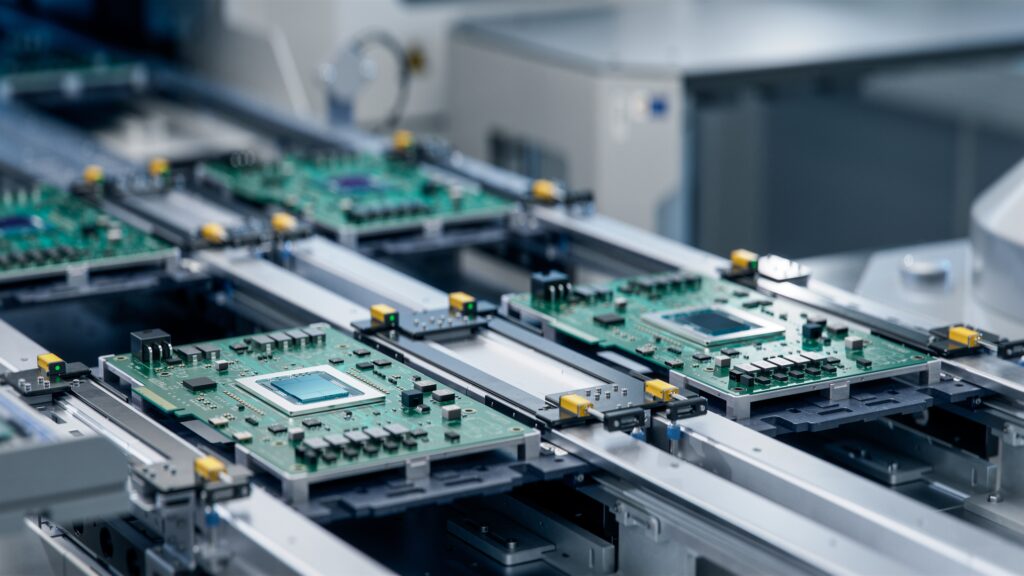
The semiconductor industry is a cornerstone of modern technology, encompassing the design, fabrication, and testing of microelectronic devices essential for everything from smartphones to advanced computing systems. Key segments within the industry include chip design, silicon wafer production, semiconductor equipment manufacturing, and semiconductor assembly and testing. Precision and reliability are paramount, making calibration critical for manufacturers. Proper calibration ensures that manufacturing equipment operates within specified parameters, which is essential for maintaining the high standards of performance and efficiency required in semiconductor production. This precision helps to minimize defects, optimize performance, and ultimately support the rapid technological advancements driven by semiconductors.
In semiconductor manufacturing, several types of calibration are crucial to ensure precision and quality. These include:
1. Electrical Calibration: Ensures the accuracy of electrical test and measurement equipment, which is vital for verifying the functionality of semiconductor devices.
2. Temperature Calibration: Critical for processes such as thermal processing, where precise temperature control impacts the quality and characteristics of semiconductor wafers.
3. Dimensional Calibration: Ensures the accuracy of equipment used for photolithography, etching, and deposition, where precise dimensions and alignment are essential for creating intricate semiconductor patterns.
4. Pressure Calibration: Important for equipment that operates under specific pressure conditions, such as chemical vapor deposition (CVD) and plasma etching systems.
5. Optical Calibration: Ensures the precision of optical instruments used in wafer inspection and metrology, which are key to detecting defects and ensuring the integrity of semiconductor devices.
6. Mass Flow Calibration: Critical for the accurate control of gases and liquids in processes like doping and deposition, impacting the consistency and quality of semiconductor production.
7. Laser Calibration: Integral to processes such as photolithography and wafer dicing, lasers require calibration to ensure the precise alignment and intensity control required for accurate patterning and cutting of semiconductor wafers.
Proper calibration in these areas ensures that manufacturing equipment performs accurately and reliably, contributing to the overall quality and performance of semiconductor products.